This week, I made a first version of the mechanical components for the spin coater that will sit inside the Fabubox. This entailed welding of the spinner bowl and bottom plate of the box. Further, I designed and 3D-printed a mounting system for both the motor driving the spin-coater as well as the main rod holding the chuck inside the spin coater, which will ultimately hold samples such as silicon wafers or glass substrates to apply thin films of e.g. photoresist to.
Welding
The main structural component of the spin-coater sitting inside Fabubox is the spinner bowl attached to the bottom plate of the box. This should be made of organic solvent-resistant material, such as stainless steel. For this prototype, we used a generic piece of thin sheet metal that was available in the CBA shop. The parts required for the spinner bowl and bottom plate are illustrated below.
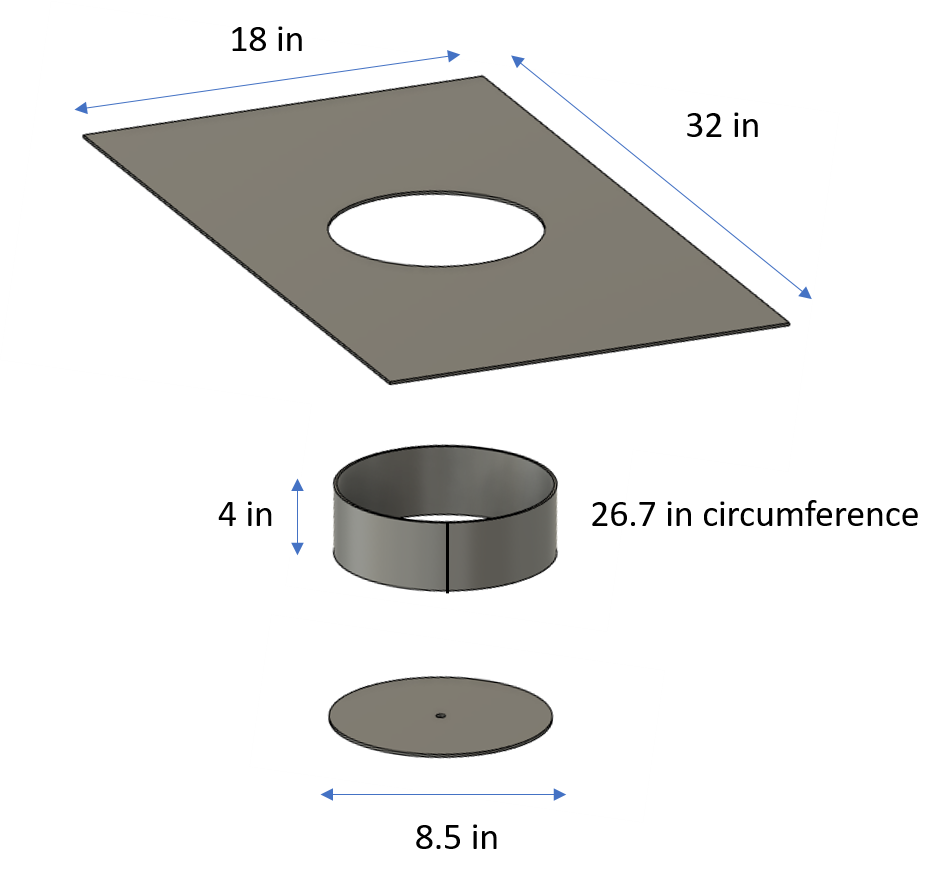
Starting from a single piece of sheet metal, with Alfonso's help, I cut the original sheet into the pieces shown above on the Fablight laser cutter.
The resulting pieces are shown below.
Next, the piece of sheet metal that will make up the bowl is bent into a circular shape.
A time lapse of the MIG welding process putting all the pieces together is shown below.
The resulting bottom plate and spinner bowl structure is slightly warped but for a first attempt came out very nicely.